新闻媒体
如何设计拉伸环,才能降低制罐厂的断罐率?
2025-02-18
变薄拉伸工艺是制造两片铝罐身的关键步骤。在拉伸过程中,通过逐渐减小罐身外壁的直径,使金属坯料成型并减薄至罐身的最终尺寸。
由于罐身的体积在整个拉伸过程中保持不变,因此要通过增加罐身的长度来实现减薄。
那么,在拉伸环设计中要注意哪些方面来保持低断罐率,优化整条生产线的性能呢?
正确的拉伸环设计在生产高质量罐身且降低断罐率方面起着至关重要的作用——低断罐率指的是因罐身金属撕裂而被排除的百分比。
几何轮廓的重要性
在拉伸罐身时,使用三个连续的拉环来逐步减少罐身厚度,直至达到薄壁和厚壁的目标厚度。典型的是铝材厚度从0.260mm或0.270mm减至0.150mm或更薄的厚壁厚度,薄壁厚度则减至0.100mm。由于厚度的减薄是通过压缩应力实现的,因此需要适当的几何轮廓,以便在易拉罐成型时,在冲头和拉伸环之间保持和分配适当的径向压力。
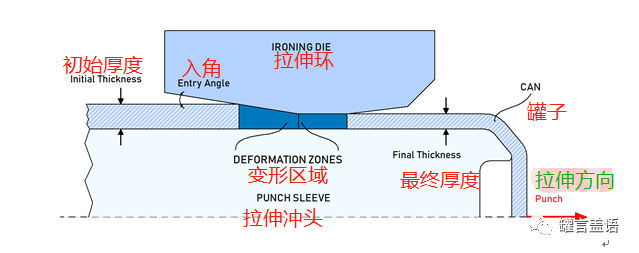
图1 变薄拉伸过程可使罐壁发生从较厚的初始厚度逐渐至较薄的最终厚度的永久塑性变形
考虑因素之一:拉伸环减薄率
减薄率(r)是一个百分数,计算公式为:
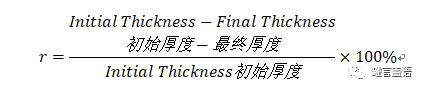
两片罐的罐壁厚度通常是从0.260~0.270mm减少至0.100mm(约从0.0102英寸减少至0.0039英寸)。这意味着总减薄率高达60%以上,无法从单环完成整个过程,否则罐子会破裂,所以通常需要3个连续的减薄拉伸环(ironing die)来完成3个不同变薄拉伸过程的减薄,即我们统称的模具包拉伸配比。
每个减薄拉伸环标准的减薄率推荐值如表1所示。需要说明的是减薄率可以根据所生产的罐的类型和拉伸机冲程长度而有所不同。
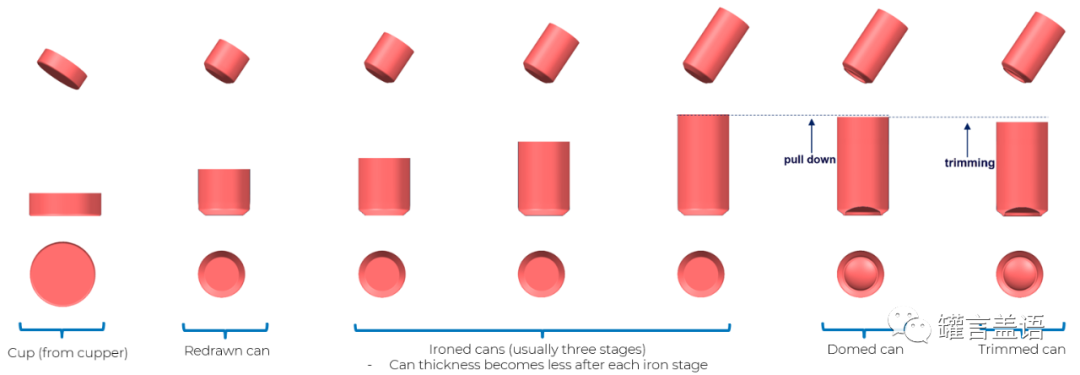
图2 DWI罐成型示意图。从左至右,分别是冲杯、再拉深(伸)、三次罐壁减薄拉伸、罐底成形、罐口修边工序
考虑因素之二:径向压力
除了减薄率,还有考虑以下因素以构建一个优化的模具包拉伸配比。变薄拉伸过程是通过压应力(compressive stresses)使罐子变形,所以在罐子成型时拉伸冲头和变薄拉伸环之间需要保持一个适宜的径向压力。这对于3号环尤其重要,以避免在罐子外部出现痕迹。
考虑因素之三:金属材料各向异性
由于罐料金属通常是铝合金,具有依赖于变形方向的特性(也称各向异性)。这种特性导致最终的薄壁厚度要比3号环上的间隙更厚。因此,必须考虑金属的特性以构建准确的拉伸配比。
表面光洁度的重要性
拉伸环的表面光洁度对拉伸质量有着直接的影响。为获得最佳的拉伸性能,拉伸环工作区域(入角和工作带)的表面光洁度应尽可能接近0微英寸 (µin)。较粗糙的工作区域会增加罐身和拉伸环之间的摩擦力,并减小罐身和拉伸环接触产生的径向压力,这两者都会增加断罐的风险。
粗糙的工作区域也会导致拉伸环的磨损加剧。由于三号环减薄至目标厚度的工作量更大,所以其也承受了更大的摩擦力。如果不优化拉伸环的表面光洁度,就会缩短拉伸环的工作寿命,并导致增加更换拉伸环的停机时间,有时仅运行几个小时就需要更换拉伸环。
免责声明
本文提供的资料部分来源网络,包括但不限于文字、图片、音频、视频等来源于第三方或网络信息,转载目的在于分享和传递行业信息,仅供用户浏览,但我们无法确保信息的完整性、即时性和有效性。若在使用过程中产生的侵权纠纷等问题,请及时联系删除,对此不承担任何责任。